Paper in the Lakes
Enthusiastically ensuring a seventh generation of papermakers embraces the future
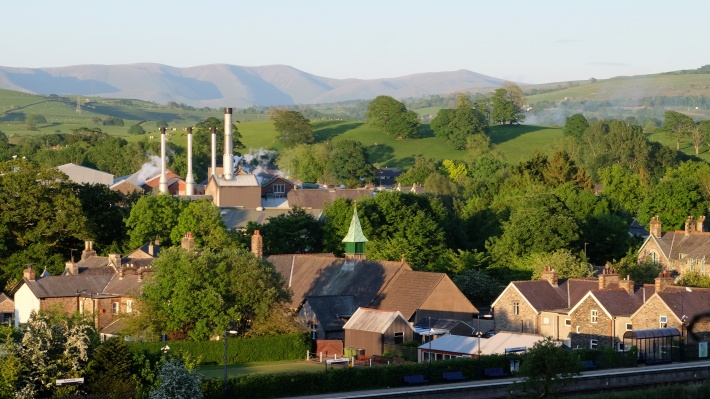
Words: Jane Audas
Photography: Mark Cropper
The paper-making hub of England is tucked into the ridiculously luscious Lake District, where everything (to a city dwelling bibliophile) looks like a book cover. ‘James Cropper’ has been making paper at the Burneside mill near Kendal, Cumbria, since the Cropper family bought the business in 1845 – although paper has been made there since the mid-18th century. Today the company’s chairman is Mark Cropper. Behind him, six generations of his family had their hands on paper here.
Mark hasn’t always worked with paper. He had a career in renewable energy in London. He left that in 2008 to set up a business building small hydro-schemes. “I like making things, creating something out of nothing.” But the pull of the Lakes and the family business proved too strong to resist, and eventually, in 2013, he was back in Burneside for good.
Mark’s office (overlooking a small garden full of just-tilting tulips when I visited) is a converted coach-house. The shelves are packed with interesting books on design, paper, textiles, patterned papers (some of which announce their insides with lovely French dominoté paper spines), wallpapers, papyrus (the paper before paper) and woodcuts, among other subjects. Only a squash of well-used Ordnance Survey maps of the area breaks the run of spines. The rest of the office contains things connected with the paper-making business, and things not: Edwardian book-paper catalogues, nice small Superbrand boxes in recognisable colours, an old billhead with curled calligraphy. They’re all beautifully laid out, by size in small, contained piles, often topped with a piece of decorative pottery. Robust pieces of locally made treacle-coloured 17th century furniture is also dotted about – adding weight to the visual story.
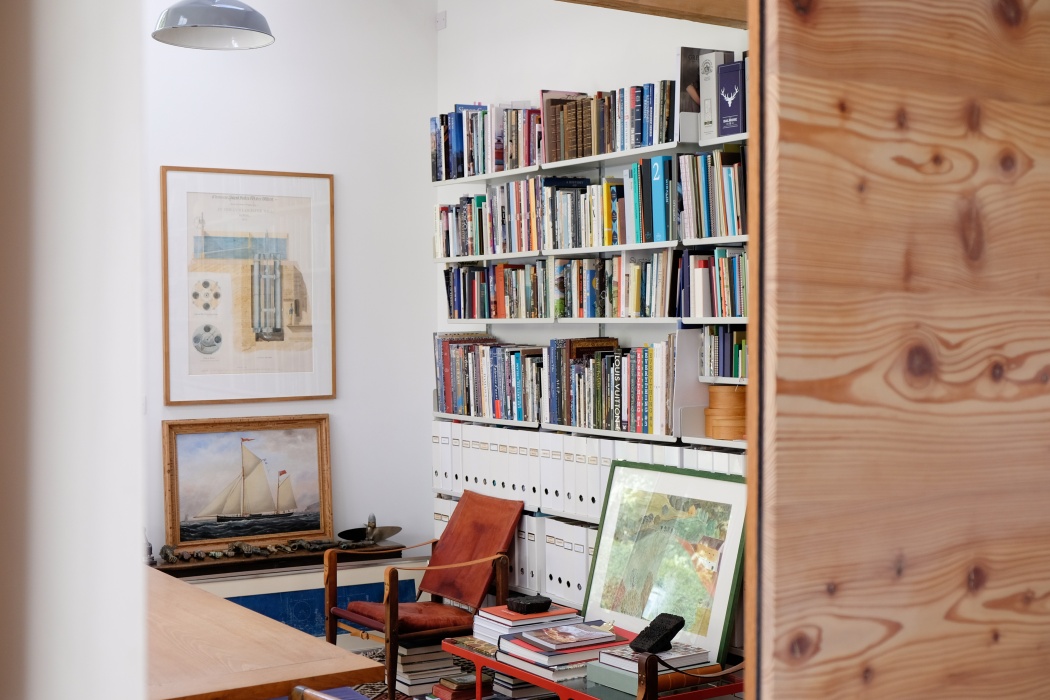
The 606 shelving system here was bought for the London office of Mark’s nascent hydro company in 2008. He thinks he probably originally spotted Vitsœ in a magazine, drawn by its pared-back aesthetic: “It matters how things look”, he says. When moving his 606 shelving to the Lakes, he recalls that he was rather surprised to be able to get all the packaging back from Vitsœ to facilitate the move: “I remember thinking at the time that it was really unusual – if not a little odd – just how hands-on their customer service was.” Since then, more 606 shelving has made its way to Burneside.
‘James Cropper’ now consists of three divisions: Paper, Colourform and Technical Fibre Products (TFP). In Paper they make traditional papers - for printing on, for artists to paint on, that sort of thing. Or you can have a bespoke paper made choosing a texture, fibre blend and shade to suit. They have recipes for over 200,000 colours in their digital colour cookbook, including 184 shades of black and 62 shades of white, for those of us who appreciate nuance. A lot of these tailor-made papers are used by luxury brands; the paper for those bright yolk-yellow Selfridges department store carrier-bags that you see bobbing down London’s Oxford Street came from the Burneside mill.
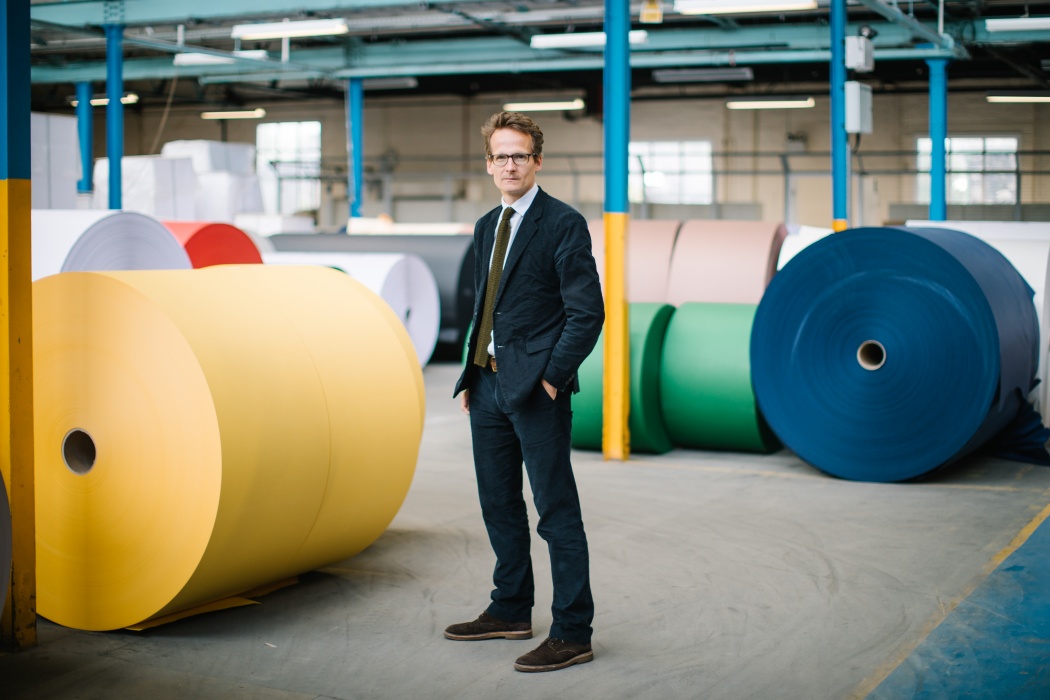
The other two strands of the business are more closely aligned to Mark’s innovation and sustainability credentials. In the early days of his return to the family business, he established a technology and innovation department at Burneside. It began as four people in a room coming up with new ideas. Their thermoform pulp, named Colourform, is made into three dimensional shapes. It is a ‘disruptive product’ for replacing plastics in packaging and a lightweight alternative to cardboard boxes. One of its first major outings was as an award-winning bottle wrap for Ruinart champagne. Replacing the bulky box, the texture of the bottle’s new tight-fitting coat (which looks rather like a silkworm’s cocoon) was based on the chalk walls of the distillery cellars in Champagne, France. And, keeping up the glamour quotient, they’ve just wrapped Dries Van Noten’s eponymous make-up and perfume line with it, too.
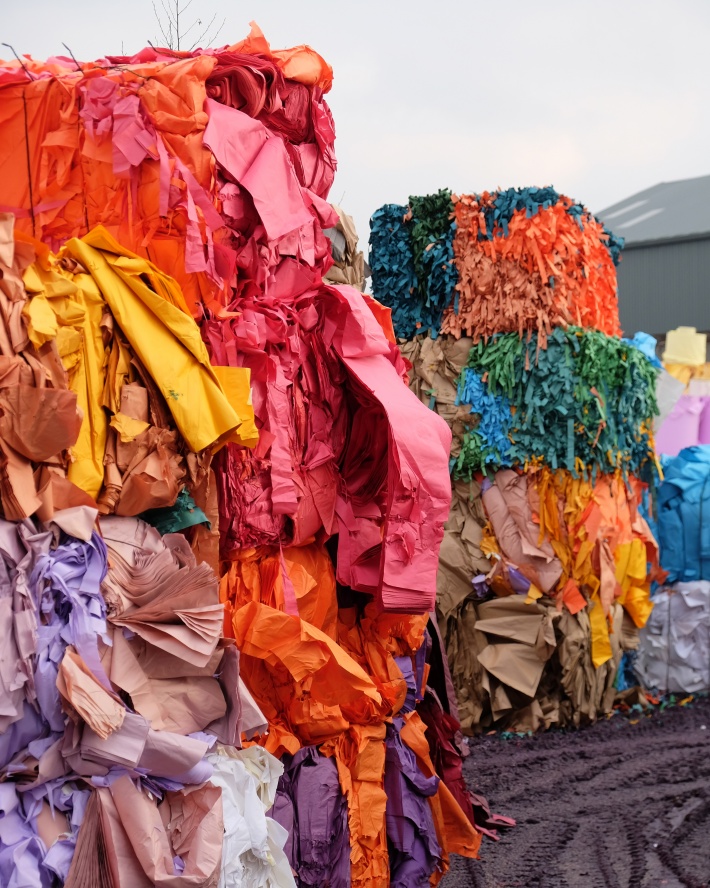
The third strand of the business is materials made from carbon fibre (and other things) produced under the name: Technical Fibre Products (TFP). Known as – taking back down the glamour quotient – ‘wet-laid nonwovens’, these materials do clever, clever things. “They can conduct, insulate, protect against fire or can carry the smoothest paint finish imaginable on the bonnet of a Lamborghini. We make critical materials and components for hydrogen electrolysis and fuel cells, wind turbine blades and carbon capture.” Mark has an air of ‘Professor Branestawm’ about him when talking about TFP; but without the patched wool jacket and crackling hair. He seems to be thinking about the future a lot, accepting of the fact that changes take time – but that’s no reason not to make them. “We are constantly reinventing ourselves. We have to think about new markets and new ways of doing things. It’s absolutely not by chance that we are still here in an industry that (basically) has mostly died in this country.”
Next, for Mark, is embracing and investing in the tradition of papermaking as a hand craft. In 2020 they opened a hand-made paper mill in a converted cow-shed. The expertise and conservation-paper-making know-how was handed over by the last paper makers in Ireland at Griffen Mill – which was relocated to Burneside in 2022. Griffen handmade papers were initially designed for the repair and conservation of books, each sheet with four true deckle edges. They are already being used by some impressive archival institutions across the world – like the British Museum and United States Library of Congress – and also by private presses, bookbinders, and other paper-inclined people, as word spreads.
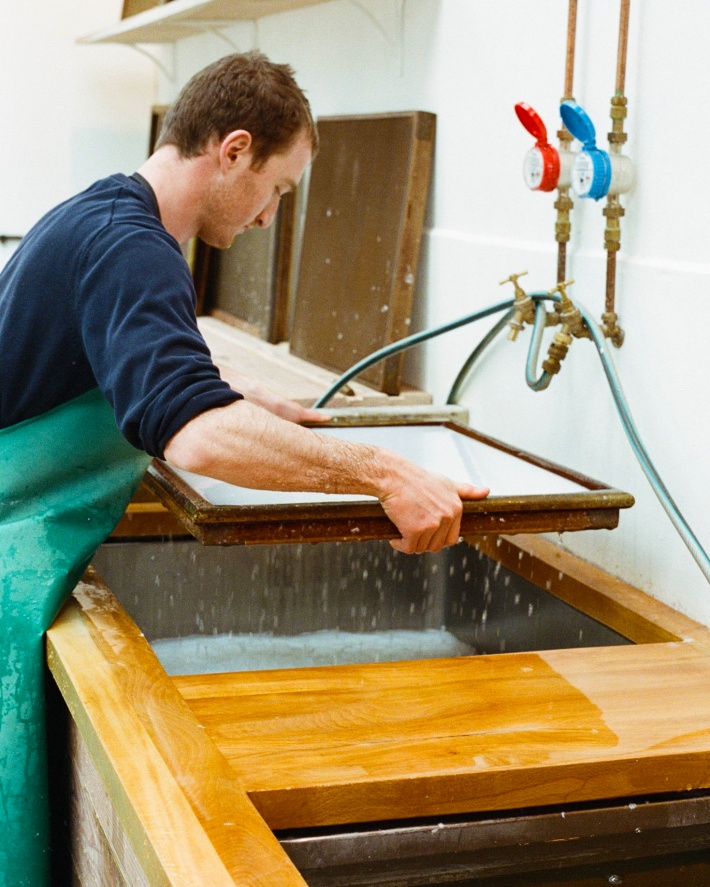
The hand-crafted papermaking is part of Mark’s newest project, the ‘Paper Foundation’, a charity founded to protect paper arts and heritage. He is currently converting the old Cropper family house, Ellergreen, into an archive, library, bookbindery and artist studios. This summer, the first archive room was completed, full of antique paper moulds nicely housed on particular shelves. The room also contains intriguing plan-chests holding patterned papers and paper-related pretties, safe out of the unforgiving sun. The intention is to welcome obsessives, to research, attend workshops and generally (or rather, specifically) bond with like-minded people over all-things paper.

For Mark, the ‘Paper Foundation’ addresses his worries over the position and importance of paper in today’s world: “Paper is one of the most remarkable materials in the history of the world but what do people do to celebrate it? How is its heritage looked after? What about all the other arts and crafts that depend upon it? Do people even think about this? No they don’t.” Mark began salvaging paper-making equipment around 2015, finding equipment in old mills all around the country, many of them closed for decades. At that time they only had five historic hand-making moulds that related to the Cropper family business. Mark has since rescued over 800 moulds (so far), many of which are perched on those shelves.
Mark’s experience of renewables is implicit in all these endeavours. He is making sure ‘James Cropper’ is forward-thinking in terms of design, yes, but also that they are future-proofed in terms of production. Over the years that he has been back in Burneside, he has been working on hydro schemes across the Lake District, a place where rain is not hard to find. And on solar-energy projects too, a bit more weather-precarious you might (wrongly) have assumed. In 2015 he founded ‘Burneside Community Energy’ to finance solar energy panels on the mill rooftops, with returns spilt between the community and local shareholders. “I just want to do more and more of that. I’m in it for the long haul.” There are also plans afoot to fully decarbonise ‘James Cropper’ by 2030.
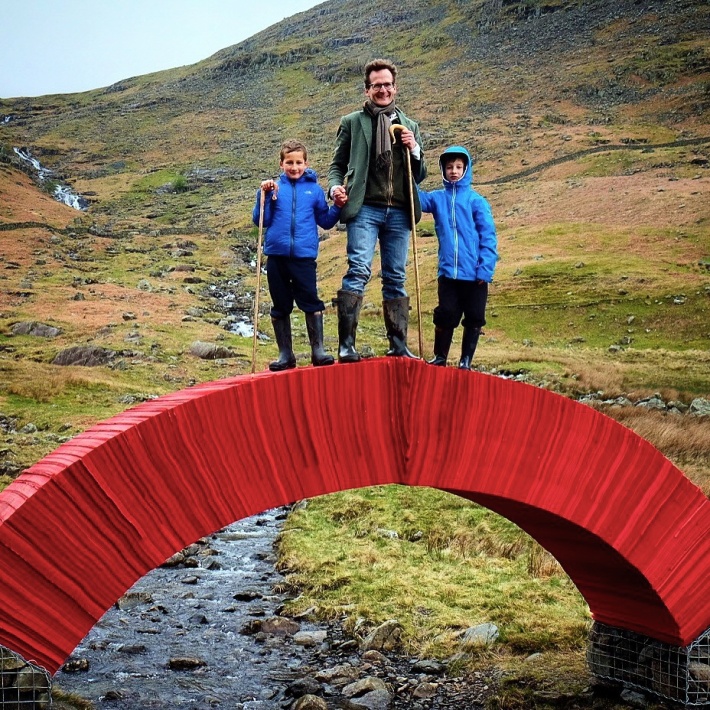
If you think about it – for a material so integral to the country’s history and culture – the United Kingdom really should have a paper hub of some sort. Mark’s ambition is to ensure the ‘Paper Foundation’ preserves paper arts and heritage for the future. There is something so right and proper about building that ambition in Burneside, where paper overlays everything they do and have done for centuries. This is a place where they get paper. And who better than Mark Cropper to see to it that we all have the opportunity to get it, too?